Construction
Great SuDS designs can be let down by poor construction. Whilst constructing SuDS does require different skills than those usually used for traditional drainage approaches, they are generally no more difficult to construct. SuDS construction usually only requires the use of fairly standard civil engineering construction and landscaping operations, such as excavation, filling, grading, topsoiling, seeding, planting and the like. While these aspects aren’t particularly difficult, their difference does require good communication between the designer and construction team and appropriate supervision.
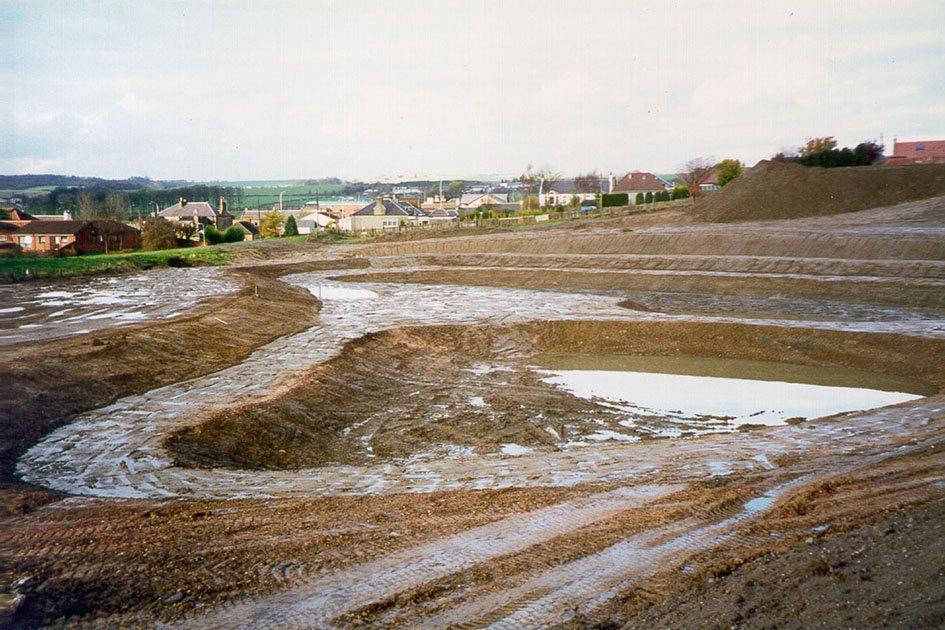
The design process should also be mindful of the construction process and ensure that there is adequate access and that the design process properly informs the construction programme as well as pollution, sedimentation and erosion control. Design will also have a bearing on the availability of materials too, as it is likely to be easier to construct and maintain SuDS if the materials used are easy to procure and source.
Key considerations
There are some specific considerations that are usually applicable to most SuDS components, and these require changes to conventional construction practices and procedures, as described in table 1.
The SuDS manual (C697) and the Site handbook for the construction of SuDS (C698) provides further detail.
Table 1: Key considerations for SuDS construction
Programming
|
Normally traditional drainage is one of the first elements of infrastructure constructed on site. For SuDS, although the form of the drainage will be constructed during the earthworks phase, final construction should not take place until the end of the development programme, unless adequate provision is made to remove any silt that is deposited during construction operations, and refurbish any areas that have been subject to over-compaction, siltation etc.
The contract is likely to stipulate establishment of landscaping vegetation, and sediment removal sometime after site works have been completed and prior to commencement of the maintenance period.
|
Pollution and sediment control
|
Surface water runoff from the construction site should not drain into SuDS components unless it has been allowed for in the design and specification. Construction runoff can be heavily laden with silt, which can clog infiltration systems, build up in storage systems and pollute receiving waters. No traffic should be allowed to run on permeable surface components if it is likely to cause clogging of the pavement surface or result in over-compaction.
|
Access and storage areas
|
Traditional car parking and other paved areas are usually constructed (or partially constructed) during the initial stages of the development, and then used as access roads and storage areas. If permeable surfaces are proposed, pavement construction should be carried out at the end of the development programme, unless adequate protection is provided to prevent clogging or blinding once it has been constructed, otherwise rehabilitation to remove clogging (i.e. suction sweeping for permeable pavements) may be required.
|
Skills and understanding
|
The contractor and all relevant operatives should have an understanding of the purpose, operation and function of the SuDS components to ensure appropriate construction practice and protection is used. This relates to the conveyance (gradients), infiltration (quality of soil) and storage of surface water runoff.
|
Infiltration system protection
|
If SuDS components are to be lined, the use of hardcore for structural purposes below the level of the liner can be accepted. However the use of hardcore is not advised if infiltration is intended, due to the high proportion of fines generally present. Sensitive ground, such as Chalk, may require the use of total exclusion zones for construction traffic to prevent compaction and other damage to the ground that will affect the infiltration performance. This may include protection from runoff during construction if the component is located at a low point on the site. Risks primarily relate to compaction and siltation of infiltration components.
|
Landscaping
|
The importance of good landscaping should be emphasised. As SuDS are normally at, or on the surface attention to detail and aesthetics must be given a high priority. The seasonal and physical requirements of planting and establishing vegetation and prevention of soil erosion should be programmed appropriately. Appropriate operative skills with an understanding of all aspects of vegetation are required.
Appropriate attention to detailing and ground levels for components should prevent any overland sediment wash off during high intensity rainfall events, or groundwater seepage during wet periods. It should also allow the appropriate overland flow of water around the SuDS scheme, ie water flows downhill.
|
Erosion control
|
Before runoff is allowed to flow through on the surface vegetated SuDS components (eg swales) they should be stabilised by planting or temporary erosion protection. This will reduce erosion and the clogging of other parts of the system by the entrained silt.
|
Handover inspection
|
Provision should be made in the construction contract to review the performance of the SuDS when it is completed, and to allow for minor adjustments and refinements to be made to optimise the physical arrangements, based on observed performance.
Suitable site supervision and inspection is also useful to ensure the SuDS components and scheme have been constructed as designed.
|
Specification and bills of quantities
|
Designers should highlight particular matters associated with the above points that are likely to impact the operation and performance of specific SuDS systems. The type of specification and/or bills of quantities will depend upon the form of construction contract being used for the specific project.
|
Inspections
Inspection during and after the construction of SuDS components and the overall scheme should be carried out to ensure that the system is being constructed correctly, and that design assumptions and criteria are not invalidated, for example, by the construction methods used, by changes made on site or by variations in ground conditions.
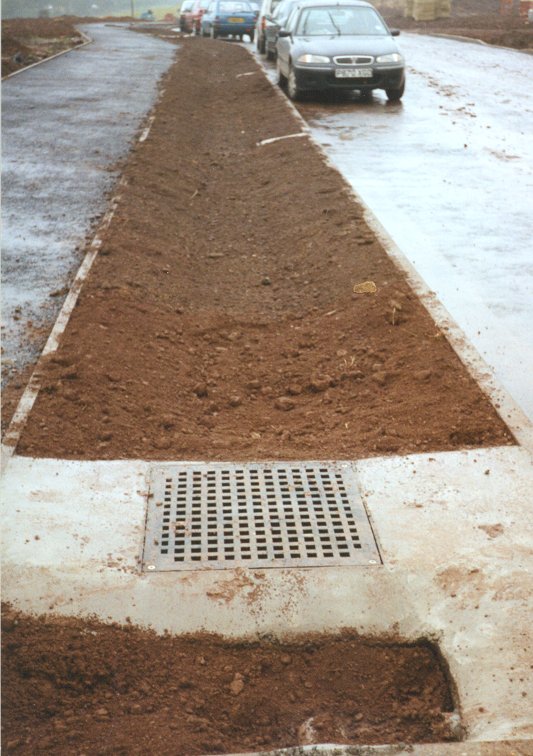
You get what you inspect, not what you expect
(famous SuDS proverb)
These inspections should be undertaken as necessary, and it may be helpful to take photographs. As a minimum inspection could be expected to include the following:
-
Pre-excavation inspection to ensure that construction runoff is being adequately dealt with on site and will not cause clogging of the SuDS components.
-
Inspections of excavations for ponds, infiltration devices, swales, etc.
-
Inspection of manufacturers details of membranes, inlets, outlets and any control structures associated with components.
-
Confirmation of sources for materials, ie soil, planting lists and material specifications.
-
Inspections during laying of any pipework.
-
Inspections and testing during the placing of earthworks materials or filter materials.
-
Inspection of the prepared SuDS components before planting begins.
-
Inspection of completed planting.
-
Final inspection before handover to client.
The contractor installing the SuDS scheme should be made fully aware of the requirement for inspections, to time meetings and avoid work being undertaken that cannot be validated.
It is likely that any client or adopting organisation would require verification that the SuDS have been constructed in accordance with the agreed design and specification. Verification is likely to include documentation from the designer and contractor and appropriate inspection during construction.
Construction method statements
The implementation of a comprehensive quality assurance (QA) regime is fundamental to the achievement of a minimum standard of workmanship. It is generally accepted that a high proportion of the perceived failures of SuDS components are as a direct result of either poor quality workmanship at the installation stage or damage during construction.
Method statements should be kept simple and emphasise the differences from traditional construction activities, setting out the justification behind the construction programming (in relation to the drainage components), describe important construction processes, and specify the installation of critical items, eg where geotextiles and geomembranes are to be placed in the construction.
Overcoming common challenges
The majority of challenges can be overcome by a competent and appropriate contractor. There are subtle (but important) differences between a ground worker and landscape contractor. Good communication with simple plans and information is essential. Other key challenges and suggestions include:
Clogging of infiltration systems – If appropriate programming is not possible (ie phased developments), careful management of construction runoff and storage of materials should reduce the chances of binding and clogging of infiltration components (permeable pavements, filter drains etc. Rehabilitation may be necessary
Compaction – careful consideration of the construction process, program and equipment is required to ensure that the ground and soil is not over-compacted, reducing infiltration.
Communication and understanding – Effective engagement is essential. The designer or contractor should produce a construction method statement for SuDS (dealing with construction runoff, program etc). Drawings should be appropriately detailed and provide an explanation of what needs to be done and why. Often a pre-startup meeting with contractors is also helpful.
Levels – Ensuring these are correct and in accordance with the drawings is essential. There also needs to be a recognition that vegetation growth may also change the levels.
Planting – Program and time of the year will have an impact on vegetation establishment, maintenance and the general aesthetics of SuDS.
All of these challenges can be overcome, but it will save time, effort and money if they’re considered from the outset.
Guidance on construction standards for components is provided in the SuDS manual.
Read more on: